Trong xã hội phát triển hiện đại, sản xuất và tiêu dùng bao bì nhựa đã trở nên phổ biến trong đời sống hàng ngày của con người, tuy nhiên cũng tạo ra lượng nhựa thải lớn gây ô nhiễm môi trường nghiêm trọng. Một số nghiên cứu về chất thải rắn (CTR) ở những khu vực đô thị ở Đồng bằng Sông Cửu Long (ĐBSCL) cho thấy thành phần nhựa chiếm từ 3,16 - 13,63% tổng lượng chất thải rắn; hoặc chiếm đến 77% lượng chất thải có thể tái chế ở thành phố Cần Thơ.
Tại Việt Nam đã có nhiều công trình nghiên cứu tái chế và xử lý lượng plastic thải bỏ như: chế tạo vật liệu bao che từ rác thải nhựa; xử lý CTR bằng công nghệ MBT-CD.08; xử lý CTR bằng công nghệ seraphin. Các biện pháp xử lý và tái chế này đã đem lại kết quả khả quan về mặt kinh tế và môi trường, nhưng vẫn chưa xử lý hoàn toàn lượng nhựa đã thải ra môi trường.
Để có thêm phương pháp khả thi và hiệu quả để tận dụng nguồn phế thải nhựa, nhóm nghiên cứu trường Đại học Cần Thơ tiến hành “Nghiên cứu tận dụng rác thải nhựa gia công bê tông làm vật liệu xây dựng” nhằm tạo ra vật liệu xây dựng mới thân thiện với môi trường và góp phần giảm thiểu lượng plastic đưa ra môi trường.
Nhựa được thu gom, sau đó rửa sạch và phơi khô. Tiếp theo nhựa được xử lý nhiệt bằng cách dùng bàn ủi ép (đặt miếng nhựa ở giữa 2 miếng tole mỏng sau đó đặt bàn ủi lên) đến kích thước đồng nhất (2 - 3 mm), tiếp đến cắt những mẫu nhựa này đến kích thước 3x3x3 mm để giúp phân bố nhựa đều hơn vào mẫu cấp.
Nhựa đóng vai trò cốt liệu thay thế cho cát trong hỗn hợp cấp phối. Do chưa có nghiên cứu tương tự nào được tiến hành, việc xác định thành phần cấp phối được đề nghị dựa vào định mức cấp phối vật liệu cho vữa bê tông.
Cường độ của vật liệu phụ thuộc vào nhiều yếu tố như thành phần, cấu trúc, phương pháp thí nghiệm, môi trường, hình dáng, kích thước mẫu. Do đó, để so sánh khả năng chịu lực của vật liệu cần phải tiến hành thí nghiệm trong cùng điều kiện. Cấp phối 1: thí nghiệm với cấp phối này được tiến hành nhằm theo dõi sự thay đổi của cường độ khi thêm thành phần nhựa vào mẫu thử. Cấp phối 2: thí nghiệm này nhằm khảo sát sự biến thiên của cường độ khi tăng lượng xi măng lên. Trong cấp phối này các thành phần cát, nước, nhựa vẫn giống cấp phối 1, riêng lượng xi măng được tăng lên 10%.
Kết quả kiểm tra mẫu cấp phối 1: Sự biến động của cường độ chịu nén theo % nhựa thêm vào được chia làm 3 giai đoạn:
Giai đoạn từ 0 - 10% nhựa: Khi tăng tỷ lệ nhựa lên thì cường độ chịu nén của mẫu cũng tăng dần, nếu mẫu đối chứng (0% nhựa) có cường độ chịu nén là 19,9 MPa thì mẫu 10% nhựa có cường độ chịu nén là 22,2 MPa. Ở tỷ lệ 5 - 10% thành phần nhựa đóng vai trò chịu lực giúp gia tăng cường độ chịu nén của mẫu.
Giai đoạn từ 10 - 30% nhựa: Trong giai đoạn này cường độ chịu nén của mẫu giảm dần đến mẫu 30% nhựa (có cường độ thấp nhất là 20,1 MPa). Mặc dù giảm xuống nhưng so sánh với mẫu đối chứng 0% nhựa thì cường độ chịu nén từ mẫu 10 - 30% nhựa vẫn cao hơn. Vì thế, ở mẫu 10 - 30% thành phần nhựa vẫn tham gia vai trò chịu lực giúp gia tăng cường độ chịu nén.
Giai đoạn từ 30 - 50% nhựa: Khi tăng tỷ lệ nhựa từ 30 - 50% thì cường độ giảm đến mức thấp hơn so với mẫu đối chứng. Nếu cường độ chịu nén quá thấp đồng nghĩa với khả năng chịu lực cũng rất thấp, điều này sẽ làm ảnh hưởng đến chất lượng của vật liệu.
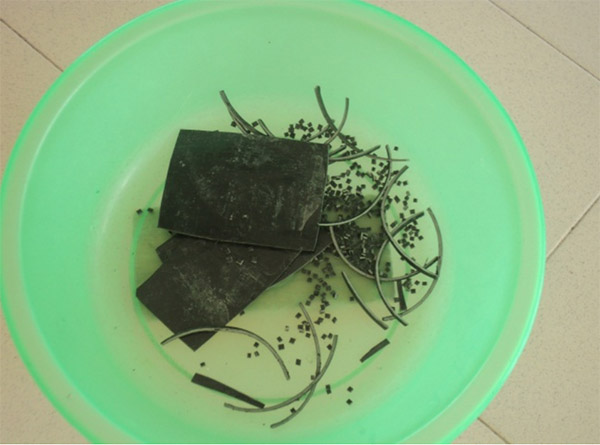
Mẫu nhựa sau khi ép.
Kết quả kiểm tra mẫu cấp phối 2: Kết quả cho thấy sự biến động theo cường độ ở cấp phối 2 có chiều hướng giống cấp phối 1. Sự biến động của cường độ không theo chiều hướng xác định nhưng có thể chia làm 2 giai đoạn:
Giai đoạn từ 0 - 10% nhựa: trong giai đoạn này cường độ chịu nén biến thiên theo chiều hướng tăng dần, so với mẫu đối chứng 0% nhựa có cường độ 21 Mpa, khi thêm vào 5% nhựa cường độ của mẫu là 24,5 MPa (tăng 16,8%) và cường độ đạt 25,3 MPa khi thêm vào 10% nhựa (tăng 19,8%). Như vậy, khi thêm vào mẫu thử từ 5 - 10% cường độ của mẫu tăng lên do nhựa tham gia vào thành phần chịu lực giúp gia tăng cường độ nén của mẫu bê tông.
Giai đoạn từ 10 - 85% nhựa: trong giai đoạn này cường độ nén của mẫu có xu hướng giảm dần khi tăng tỷ lệ nhựa. Tuy nhiên, so sánh với mẫu đối chứng 0%, từ mẫu 10 - 30% cường độ vẫn nằm trong khoảng phù hợp (cao hơn hoặc bằng mẫu đối chứng). Như vậy, ở khoảng 10 - 30%, thành phần nhựa vẫn đóng vai trò chịu lực và không ảnh hưởng đến cường độ của mẫu. Ở mẫu có 30 - 85% nhựa cường độ mẫu giảm và thấp hơn so với mẫu đối chứng, do ở tỷ lệ này nhựa không tham gia vào thành phần chịu lực của hỗn hợp bê tông. Dựa vào kết quả đo đạc của các mẫu cấp phối cho thấy:
So sánh với mẫu đối chứng 0% nhựa, mẫu được thêm nhựa vào có ưu điểm là khối lượng thể tích nhỏ hơn do thành phần nhựa có khối lượng riêng nhỏ hơn khối lượng riêng của cát. Vì vậy, khi thay thế lượng cát bằng nhựa khối lượng thể tích của mẫu sẽ giảm xuống. Khi tăng lượng nhựa lên 5% thì khối lượng mẫu bê tông sẽ giảm 2%. Nếu áp dụng tỷ lệ 30% nhựa thì khối lượng của mẫu thử sẽ giảm 12% so với mẫu đối chứng.
Kết quả cũng cho thấy, không nên áp dụng tỷ lệ > 30% nhựa thêm vào vì sẽ làm giảm cường độ, không tạo được khả năng kết dính cao trong bê tông. Cả hai kết quả nén mẫu ở cấp phối 1 và cấp phối 2 đều ghi nhận tỷ lệ nhựa thêm vào 30% vẫn cho cường độ bê tông đạt yêu cầu.
Nghiên cứu đã đề xuất giải pháp xử lý nhựa thành hạt vật liệu để đưa vào cấp phối bê tông và xác định được lượng nhựa tối ưu đưa vào nhiều nhất mà sản phẩm bê tông vẫn đạt chất lượng về cường độ chịu nén theo quy chuẩn Việt Nam. Kết quả thử nghiệm cho thấy khi thay thế cốt liệu cát bằng vật liệu nhựa với tỷ lệ 5 - 30%, mẫu bê tông đạt yêu cầu sử dụng cho các công trình xây dựng. Như vậy, rác thải nhựa có thể tận dụng để chế tạo vật liệu xây dựng mới phù hợp theo định hướng của quốc gia về phát triển vật liệu thân thiện với môi trường, đồng thời giảm thiểu lượng nhựa đưa vào dòng thải tránh gây ô nhiễm môi trường.
VLXD.org (TH/ CNMT)